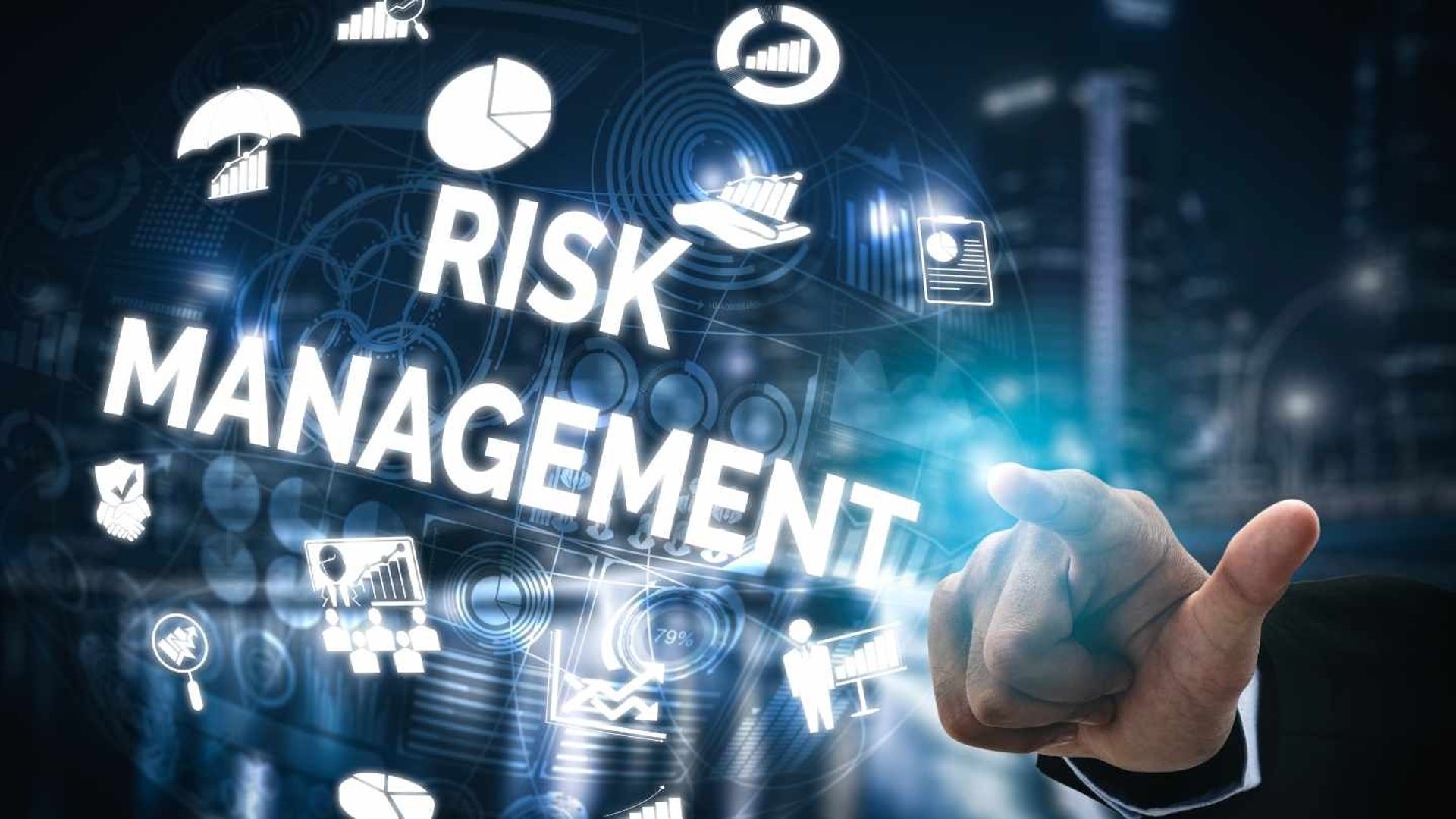
Safety Management at Eleter Projects
Site Safety Planning
Our site safety planning is a proactive process that begins well before construction starts:
Site-Specific Safety Plans: For each project, we develop a tailored safety plan that addresses the unique hazards and challenges of the site.
Hazard Identification: We conduct thorough site inspections to identify potential hazards, including environmental, operational, and health risks.
Safe Work Method Statements (SWMS): We prepare detailed SWMS for high-risk construction work, outlining step-by-step procedures to perform tasks safely.
Emergency Response Planning: We develop comprehensive emergency response plans, including evacuation procedures, emergency contact information, and first aid protocols.
Traffic Management Plans: For sites with vehicular traffic, we create detailed plans to manage the safe movement of vehicles and pedestrians.
Equipment and PPE Planning: We ensure that appropriate safety equipment and Personal Protective Equipment (PPE) are available and properly maintained for all workers.
Safety Communication Strategy: We establish clear channels for communicating safety information, including daily toolbox talks and prominently displayed safety signage.
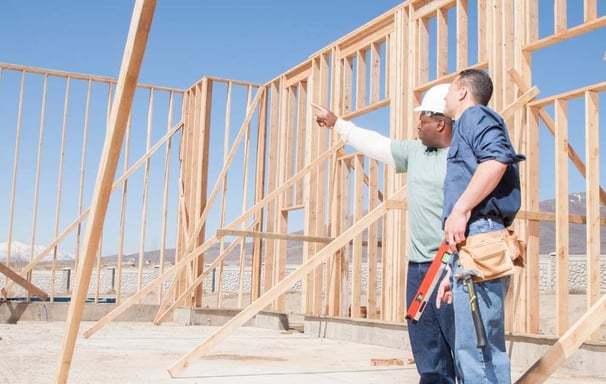
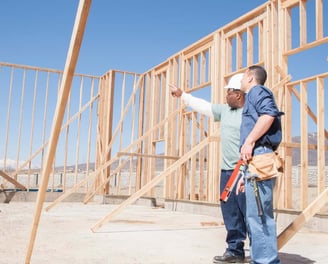
Safety Regulations and Compliance
Staying compliant with safety regulations is a top priority at Eleter Projects:
Regulatory Monitoring: We stay up-to-date with all relevant safety regulations, including WorkSafe NSW guidelines and the Work Health and Safety Act 2011.
Compliance Audits: We conduct regular internal audits to ensure our practices align with current safety regulations.
Documentation Management: We maintain meticulous records of all safety-related documentation, including permits, licenses, and certifications.
Subcontractor Compliance: We ensure that all subcontractors meet our stringent safety standards and comply with relevant regulations.
Reporting Compliance: We adhere to all mandatory reporting requirements, including incident reporting to relevant authorities when necessary.
Continuous Education: Our safety team regularly attends industry seminars and workshops to stay informed about regulatory changes and best practices.
Legal Consultation: We maintain relationships with legal experts specializing in construction safety to seek advice on complex compliance issues.
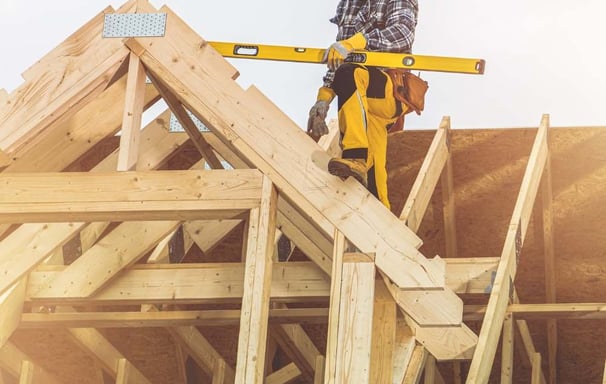
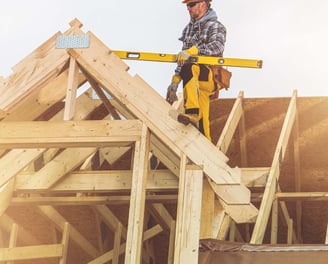
Risk Assessment and Mitigation
Our approach to risk assessment and mitigation is thorough and ongoing:
Formal Risk Assessments: We conduct comprehensive risk assessments for each project, identifying potential hazards and evaluating their likelihood and potential impact.
Hierarchy of Controls: We apply the hierarchy of controls (Elimination, Substitution, Engineering Controls, Administrative Controls, PPE) to mitigate identified risks.
Job Safety Analysis (JSA): For high-risk tasks, we perform detailed JSAs to break down the job into steps and identify safety measures for each step.
Dynamic Risk Assessment: We encourage workers to perform on-the-spot risk assessments before starting any task, empowering them to identify and address immediate risks.
Risk Registers: We maintain and regularly update risk registers for each project, tracking identified risks and mitigation measures.
Safety Observations: We implement a system of safety observations where workers and supervisors regularly report potential hazards or unsafe practices.
Technology Integration: We utilize digital tools and software for real-time risk reporting and assessment, allowing for quick response to emerging safety concerns.
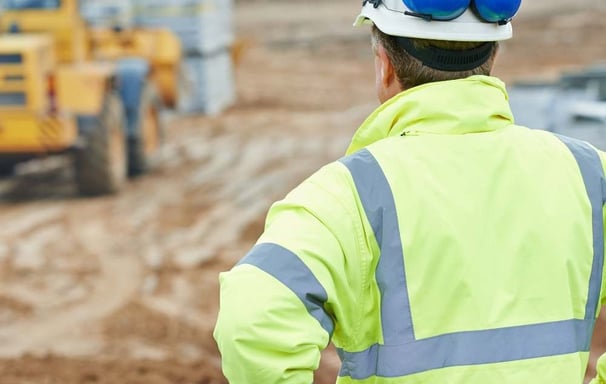
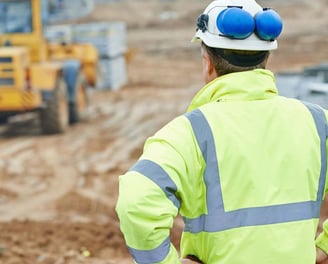
Safety Training Programs
Comprehensive safety training is a cornerstone of our safety management approach:
Induction Training: All workers, including subcontractors, undergo thorough safety induction training before starting work on our sites.
Task-Specific Training: We provide specialized training for high-risk tasks such as working at heights, confined space entry, and operating heavy machinery.
Regular Refresher Courses: We conduct periodic refresher training to reinforce safety practices and introduce any new safety protocols.
Leadership Safety Training: Our supervisors and managers receive additional training on safety leadership and creating a positive safety culture.
Emergency Response Drills: We regularly conduct drills to ensure all workers are prepared for potential emergency situations.
Toolbox Talks: Daily toolbox talks are held to discuss specific safety topics relevant to the day's work activities.
Competency Assessments: We perform regular assessments to ensure workers maintain the necessary skills and knowledge for safe work practices.
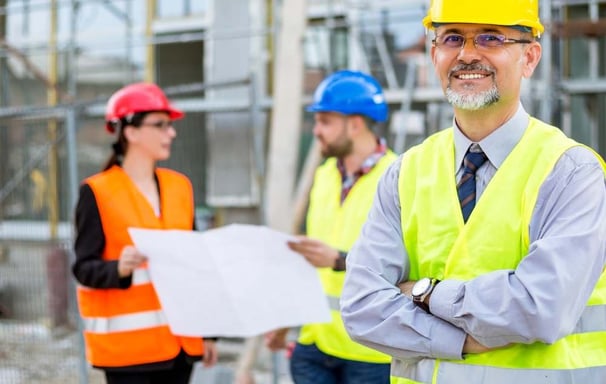
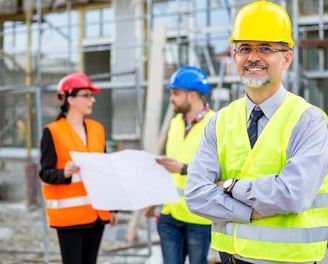
Incident Reporting and Investigation
Our incident reporting and investigation process is designed to learn from incidents and prevent recurrence:
Clear Reporting Procedures: We have established clear procedures for reporting all incidents, near-misses, and safety concerns.
Immediate Response Protocol: We have a defined protocol for immediate actions following an incident, including securing the scene and providing medical attention if needed.
Thorough Investigations: All incidents are thoroughly investigated to determine root causes and contributing factors.
Incident Classification: We classify incidents based on severity and potential impact to ensure appropriate levels of investigation and follow-up.
Corrective Action Plans: Based on investigation findings, we develop and implement corrective action plans to prevent similar incidents in the future.
Lessons Learned Communication: We share lessons learned from incidents across our organization to improve overall safety performance.
Trend Analysis: We regularly analyze incident data to identify trends and focus our safety efforts on areas of greatest need.
At Eleter Projects, we believe that every incident is preventable, and we strive for zero harm in all our operations. Our comprehensive approach to safety management, developed over 15 years in Sydney's construction industry, ensures that safety remains at the forefront of everything we do. By prioritizing safety, we not only protect our workers and stakeholders but also enhance our overall project efficiency and quality.
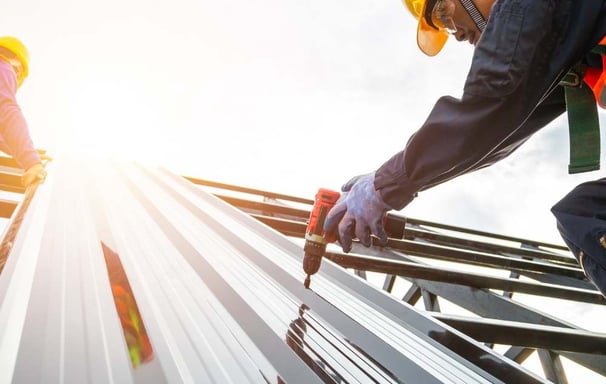
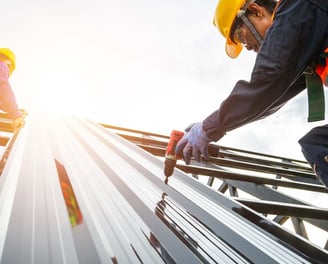
161 Parramatta Rd Annandale NSW 2038
Call Us on: 0414 738 827
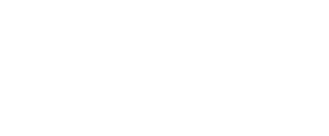
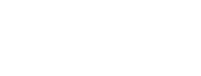
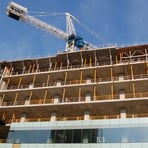
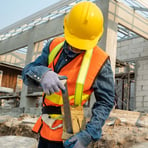
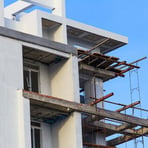
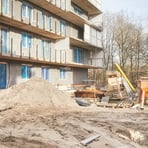
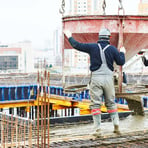
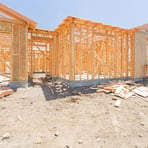
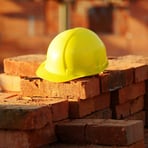
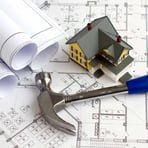
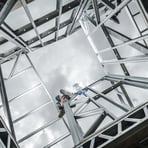
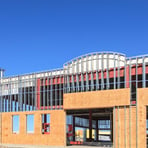
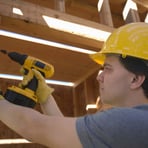
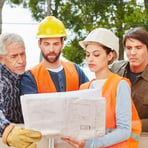
All Rights Reserved © Eleter Projects 2024