
Quality Management in Construction
Quality Assurance Processes
Our quality assurance (QA) processes are proactive measures designed to prevent defects and ensure consistent quality throughout the project lifecycle:
Quality Management Plan: For each project, we develop a tailored Quality Management Plan that outlines quality objectives, responsibilities, and procedures.
Standard Operating Procedures (SOPs): We maintain and regularly update a set of SOPs that cover all critical construction activities, ensuring consistency across projects.
Training and Certification: We invest in ongoing training for our staff to keep them updated on the latest quality standards and best practices in construction.
Supplier and Subcontractor Vetting: We have a rigorous process for selecting and evaluating suppliers and subcontractors based on their quality track record and adherence to standards.
Design Quality Assurance: We conduct thorough reviews of project designs and specifications to identify and address potential quality issues before construction begins.
Risk-Based Quality Planning: We identify high-risk areas of each project and develop specific quality assurance strategies to mitigate these risks.
Documentation Control: We maintain a robust system for managing all quality-related documentation, ensuring easy access and traceability.


Quality Control Measures
While quality assurance focuses on prevention, our quality control (QC) measures are designed to identify and correct any deviations from quality standards:
Inspection Checklists: We use detailed checklists for each phase of construction to ensure all quality requirements are met.
Material Testing: We conduct regular testing of construction materials to verify they meet specified standards and project requirements.
Work in Progress Inspections: Our quality control team performs frequent inspections during construction to catch and correct issues early.
Non-Conformance Reporting: We have a formal system for reporting, tracking, and resolving any instances of non-conformance with quality standards.
Statistical Quality Control: For repetitive processes, we use statistical methods to monitor quality and identify trends or patterns that may indicate underlying issues.
Third-Party Inspections: We engage independent inspectors for critical phases or components to provide an unbiased assessment of quality.
Quality Control Circles: We encourage our workers to form quality control circles, empowering them to identify and solve quality issues at the source.


Inspection and Testing Procedures
Our inspection and testing procedures are thorough and systematic, ensuring that every aspect of the project meets our high-quality standards:
Inspection Schedule: We develop a comprehensive inspection schedule that aligns with the project timeline and critical construction milestones.
Multi-Level Inspections: We conduct inspections at various levels, including self-inspections by workers, supervisor inspections, and formal QC inspections.
Specialized Testing: We employ specialized testing methods for critical components, such as concrete strength testing, soil compaction tests, and building envelope air tightness tests.
Non-Destructive Testing: Where applicable, we use non-destructive testing methods like ultrasonic testing or thermal imaging to assess quality without damaging the structure.
Commissioning Tests: For building systems (HVAC, electrical, plumbing), we conduct comprehensive commissioning tests to ensure proper functionality.
Documentation and Reporting: All inspection and test results are meticulously documented and reported, with clear protocols for addressing any failures or anomalies.
Regulatory Compliance Checks: We perform regular checks to ensure all work complies with local building codes and regulations.


Defect Management
Effective defect management is crucial for maintaining quality and client satisfaction:
Defect Identification: We have a systematic process for identifying defects, including regular inspections and a mechanism for workers to report issues.
Defect Classification: We classify defects based on severity and potential impact, allowing us to prioritize remediation efforts.
Root Cause Analysis: For significant defects, we conduct thorough root cause analysis to prevent recurrence.
Corrective Action Plans: We develop detailed plans for addressing each defect, including timelines and responsible parties.
Defect Tracking System: We use a digital system to track all identified defects from discovery to resolution, ensuring nothing falls through the cracks.
Client Communication: We maintain transparent communication with clients about any defects found and our plans to address them.
Post-Handover Defect Management: Our commitment to quality extends beyond project completion, with a robust process for managing any defects identified during the warranty period.


Continuous Improvement Strategies
At Eleter Projects, we believe in constantly refining our processes to deliver ever-higher quality:
Lessons Learned Sessions: After each project, we conduct thorough reviews to identify areas for improvement in our quality management processes.
Benchmarking: We regularly benchmark our quality performance against industry standards and best practices.
Technology Integration: We continuously explore and integrate new technologies that can enhance our quality management capabilities, such as digital quality management platforms and IoT sensors for real-time quality monitoring.
Feedback Loops: We have established feedback mechanisms to gather insights from clients, subcontractors, and our own team members to drive improvements.
Quality Metrics and KPIs: We track a set of quality-related metrics and KPIs, using this data to identify trends and areas for improvement.
Continuous Training: We invest in ongoing training and development for our team, keeping them updated on the latest quality management techniques and technologies.
Innovation Encouragement: We encourage and reward innovative ideas from our team that can enhance our quality management processes.
By implementing these comprehensive quality management strategies, Eleter Projects ensures that our construction projects in Sydney consistently meet the highest standards of quality. Our commitment to excellence in every aspect of our work has been a cornerstone of our success over the past 15 years, earning us a reputation for delivering superior results in the competitive construction market.


161 Parramatta Rd Annandale NSW 2038
Call Us on: 0414 738 827
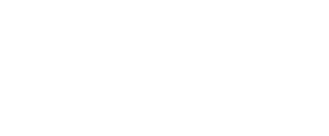
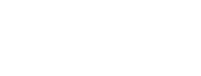
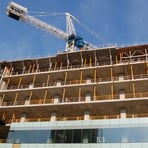
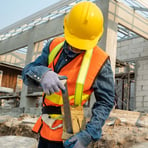
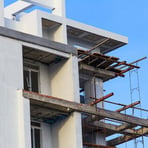
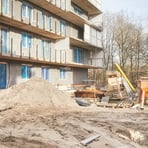
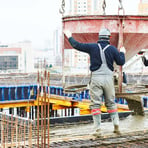
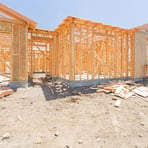
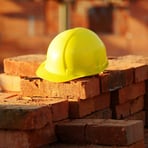
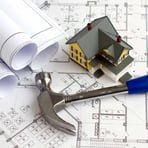
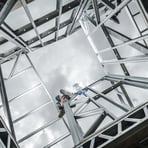
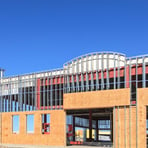
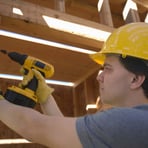
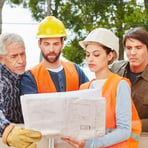
All Rights Reserved © Eleter Projects 2024